All our products meet the demands of virtually every conceivable application in the processing industry, and our name is synonymous with endurance, reliability, and excellence.
From grinding and conditioning to size reduction, our equipment solutions are engineered to meet the demands of virtually every application in processing industries.
needs of every industry
If quality and efficiency are your top priorities, CPM has what you need. Our products meet the demands of virtually every application in the processing industries. CPM is your one-stop equipment solution.
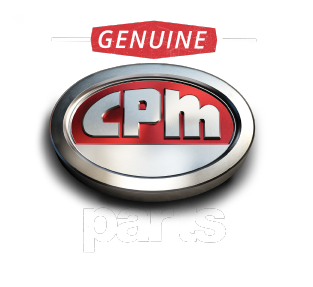
We offer customer service and sales support through a worldwide network of local agents in nearly every country. Whatever your needs, we're here to help in any way we can.